CASE STUDY: Mining Co Titanium Coils Destroyed by Closed Failures
- Pulse
- Oct 27, 2022
- 2 min read
Updated: Sep 27, 2023

Challenge:
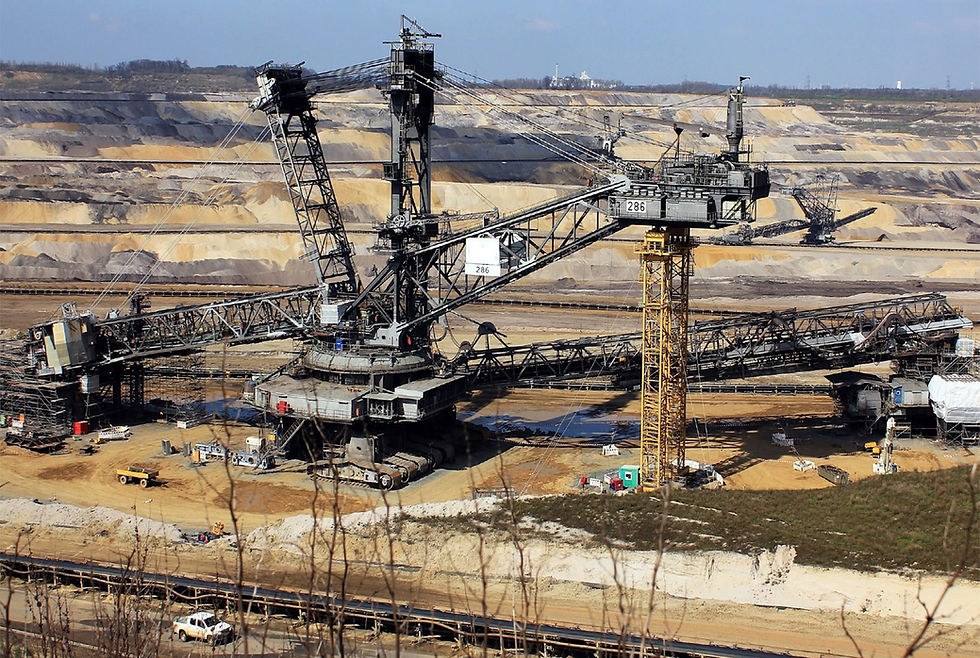
A mining company has steam to power many processes including a tank farm, autoclave and heating. They have experienced a number of cold (closed) failures which caused titanium coils to blow. Not only are the coils very expensive to replace but since they are so remote it takes time and more money to get replacement coils to the site.
While waiting for replacements production can not continue so the whole site sits idle.
Each titanium coil costs upwards of $500, but the real cost is safety and reliability
Solution:
Installing Pulse Steam Trap Monitors on all steam traps enabled the mining operation to get advance warning and turn system off before the pressure builds enough to blow the titanium coils. A new steam trap is very cost effective and swapping it out takes a minimal amount of time and effort. Cold failures are quite rare but they actually represent a more dangerous failure - a worker in the area could potentially be injured. Monitoring traps using temperature and sound allows all types of traps and all types of failures to be detected in time to be repaired.
“We experience less down time and I am relieved to not put workers at risk anymore.”
Benefits:
Titanium coils are very expensive - getting advance warning that pressure levels are increasing to a point where they would cause failures means the coils last much longer
Workers are safe and don’t have long periods of inactivity due to system shut downs
LoRaWAN technology is another essential element in these scenarios as equipment is very remote
Inspections are also much more difficult to arrange due to accessibility challenges, inspections are required much less frequently with automated monitoring devices
Both closed and open failures on dozens of different types of equipment are caught and repaired over the course of many months not just annually with inspections
Kommentare